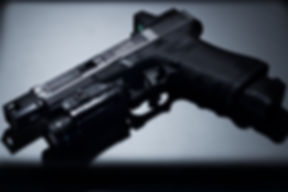
Please see our FAQ for information on our current lead times located HERE
If you have an order in the shop, feel free to conact us on its status.


Frequently Asked Questions
We will be working on expanding our FAQ to cover some of your commonly asked questions. If you don't see your question answered here, please feel free to reach out to us at namelessarms@gmail.com. We'd love to hear from you!
Lead Times Explained:
One of the most common questions we get is "what is your current lead time" which usually leads to wondering why are our lead times are where they are at. Let's dive in to this and hopefully shed some light on our processes and what factors into our lead times.
Probably the first thing to cover is that we will only ever move at the speed of quality. Quality is a term that is commonly thrown around in today's world so it is probably important to understand what we define as quality when we describe our company. Quality to us is performing the best work we can on every slide, every time. This encompasses the attention, detail and precision that goes into the machining and coatings we perform, as well as the level service we strive to provide to our customers. No one else is offering match fit precision optic milling and this level of service at our price point and we truly believe that our work stands among the best in the industry. Here are some things you can expect when sending your slide in to us for service:
-
We match fit every optic to every slide when we perform an optic cut. This results in the most secure method of attaching an optic to a slide. We do this because we want you to have the strongest possible optic interface so there is less risk of your setup failing you when you may need it the most. While this is not the fastest way to do things (this is actually one of the largest contributors to our lead times), it is the best way to do things and we don't mind the extra time and effort it takes. To read more on match fit optic cuts click here.
-
We were the first shop (and currently one of only a few) to offer Cerakote on the optic pocket only. Believe it or not, this is actually more labor intensive than applying Cerakote to the entire slide due to the multiple masking and preparation steps involved. The advantage is that this provides permanent protection to the optic pocket while being able to maintain the often superior OEM coating on the rest of the slide where it really matters. Even if no coating is selected/purchased we still perform additional steps above and beyond what others do to provide you with some measure of corrosion resistance and a clean looking optic pocket. As an example, all carbon steel slides have the optic pocket masked off, bead blasted, black oxide/cold blued, and coated with LPS3 Corrosion Inhibitor. None of these things are faster to do but they result in a better end product.
-
We strip, clean, inspect, and assemble every slide we take in for service. If there are issues with your slide or its internals we will let you know. If there are parts you want/need installed in or on your slide at the time of service (such as sights or internal components) just let us know and we are happy to do so. No charge. Ever.
-
One person, one slide at a time. That means there is one singular focus when your slide is being worked on. Our work is performed with attention to detail, precision, and quality. If it's not right, it doesn't ship.
-
Your slide is sent back with the optic already mounted properly. First, we only use American made fasteners that are sized correctly for your setup. We then apply thread locker and torque the fasteners upon assembly. We also "witness mark" your fasteners as both an indication of final QC being performed and as an indication for you to observe that your screws are staying nice and tight.
-
While we cannot zero your optic for you (that can ONLY be performed under live fire with the ammunition you plan to use), we do set everything to the centerline of your slide to speed up the zeroing process. At the same time we check the function of your optic as well as the windage and elevation adjustments to make sure they are working properly.
Now with what we have covered above, lets talk about what our lead times currently are as well as other factors that contribute to our lead times:
As of 2025 our lead times can be approximately 4 weeks for service
-
We are a husband and wife team. That's it, just the two of us. This is the other area that largely contributes to our lead times. In the shop, Nate performs all the work to every slide in addition to all of the other shop related tasks (like cleaning, equipment maintenance, repair, etc), while Heather primarily takes care of customer service, shipping, and receiving. Let's be honest, this is where other outfits have a tremendous advantage. Larger shops with larger teams and more equipment can get things done faster. As a small two person operation we can only devote ourselves (individually) to typically one task at a time. Even still, we feel we are very competitive with what the average is in the industry for the level of work and service we provide. We still have not found another shop that provides customers a match fit optic interface at the price point and timeframe we strive to maintain.
-
Optics that stray wildly from their advertised footprint specifications require programming and development of a new optic cut just like a new footprint and slide combination. This not only adds to the time required to complete your slide, but also to others in the queue. This is one of the reasons we flat out refuse to machine for some optics that we know are not quality options. We simply cannot justify spending the time on programming and delaying service to others for an optic that will not last. Other optics that fall into the "acceptable" range in terms of quality (but do not make our recommended list), also often stray from the dimensions of their advertised footprint and will take more time to complete the machining portion service work. Again, because we are a small shop, we can only do one task at a time and if we are programming, we are not machining or coating.
-
Customer service is among our highest priorities. Emails are answered primarily by Heather but if they are technical in nature then Nate will also step in to assist. If you call you will most likely be speaking with Nate. If you drop off your slide in person, Nate will be the one you meet with. We want to make sure you are speaking with the person who is performing the services on your slide in case you have any questions. We want to make sure you feel that as a customer you are important to us and that we take the time to help you arrive at the best setup for you. We pride ourselves on serving as a helpful information resource for our customers to help them make the best decisions when choosing and optic or having their slide machined, even if it ends up being with someone else or another solution all together.
-
Sometimes delays can be caused by things that are out of our control. Cerakote can go bad (we've even had brand new bottles arrive contaminated or faulty), equipment can fail, or family emergencies can happen that take precedence. We try our best to ensure that these things seldom happen or that we have backups to minimize any downtime where possible.
Finally with all that being said, lead times are of course an estimate of the timeframe to for the work on your slide to be completed. We typically machine and coat 100 to 120 slides a month so things get pretty busy for a two person operation. As previously stated, our top priority is always providing the best quality of work and service we can to the end user. We will not sacrifice the quality of our work in order to provide faster lead times, period. While we always strive to have your slide back to you as soon as we can, the quality of the work we perform is ALWAYS the top priority.
Q: What coating options are available and recommended?
A: We offer a couple options when it comes to coatings and finishes on your slide when sent in for machine work. Our recommendation is typically based on what the slide is made of, what coating is already on it, and what is the scope of the machine work being performed.
For slides sent in for optic milling we typically recommend one of two options. If the slide is stainless steel then we usually recommend a coating of LPS3 to the machined area only (which is done at no additional cost to the customer). If the slide is carbon steel then we would recommend going with optional cerakote on the optic pocket only for the most corrosion resistant option, however we still take steps to protect the machined area if no coating is purchased or desired (again at no additional cost). These steps include the optic pocket being masked off, bead blasted, black oxide/cold blued, and coated with LPS3 Corrosion Inhibitor (which holds up and works very well if maintained). On carbon steel slides LPS3 is not a permanent coating and will eventually degrade so at some point re-application or preventative maintenance will be required by the end user.
If the slide is having other areas machined (such as front serrations, windows, etc.) then the only option we will recommend and that we can perform in house is having the entire slide cerakoted. Unfortunately at this time we are not able to offer nitride or PVD coating (which are far superior to Cerakote). If you want us to perform the machining but have your slide coated by another entity we totally understand and in no way take offense to that. It's all about what works best for you.
One thing we want to make clear to our customers, Nitride and PVD are superior in terms of durability to cerakote (it is also what most OEM's are using these days). While we still believe that cerakote is a fantastic option for re-finishing (it is also used by many OEM's and reputable shops) it will not provide the same level of wear resistance and protection as nitride and PVD. Each of the coating options have their advantages and disadvantages. For example, if you want your slide finished a certain color, pattern, or design, then cerakote may be your only option. However, if you already have a black nitride slide it wouldn't make sense to have it cerakoted graphite black as you would be downgrading the coating in our opinion. It also doesn't make sense to have your entire slide nitrided (if it already was nitrided, PVD coated, or NDLC) if the only machine work performed was optic milling as cerakote will be less expensive, have a faster turnaround, and provide permanent protection to the machined area all while keeping the OEM finish on the rest of the slide.
Q: If I have a match fit optic cut, what happens if I need to replace my optic and the new one doesn't fit?
A: If you new replacement optic does not fit because it runs on the larger side of the tolerance than your slide will need to be re-machined for the new optic. All you need to do is let us know and send your new slide and optic in for us to perform the re-work. We will re-machine the optic pocket to accommodate the new optic as well as perform any re-coating as needed. The only thing you pay is the return shipping back to you once the work is completed, we don't charge you again for machining/coating.
We fully acknowledge this may be viewed by some as somewhat inconvenient but we are 100% of the opinion that the mounting security of the optic is far more important and superior to an optic pocket that is machined intentionally oversized just so it can accommodate a wide range of optic sizes/tolerances (and is therefore less secure). In the end we will always recommend picking a quality optic and having it match fit to the slide which will set you up for long-term success with setup that can go the distance under hard use.
Q: Why isn't your address on the website and how do I get it?
A: We get this question a lot. We removed our address from the website because in the past we would have customers that would send in their slides without any notice or without placing an order. We also have had a lot of customers in the past send in slides without optics, or slide and optic combinations we do not machine for - again without notifying us. So how do thing work now?
When you place an order on our website you will receive two emails. One is a confirmation of your order and the second will contain a PDF attachment with our packaging recommendations, instructions on what to send in, along with the address you will send your slide and optic in to. This has largely alleviated the issues we encountered in the past so we continue this practice today to help us with tracking work as it arrives to the shop.
Q: I don't see my slide and optic combination on your website. Will you machine for it?
A: That really depends on several factors. One of the biggest is if we have the time to program and develop the optic cut. When we are busy our focus is on completing the work moving through the shop in addition to the other aspects of running a business. Sometimes we simply just do not have the time to allocate to program development. If we do know of another reputable shop that can machine for the slide and optic combination you are looking to have mated together, we are always happy to refer you to them as we always want help you find the best solution - even if it is somewhere else. Other times when things are slower & we can take on such tasks, we are more than happy to develop new programs.
Another factor is if the slide can even accommodate an optic cut or specific footprint. There are a lot of slide designs that simply do not lend themselves to being machined to accept a specific optic footprint or even an optic at all. The plain fact is that some pistols are just meant to serve as iron sight only platforms.
Lastly, there are simply some platforms that we are just not familiar with enough to take on. If there is a high enough demand and we suspect it can be done, we will usually procure one to inspect, measure, test and develop the programming to offer it to our customers. After all, you don't have to give us an excuse to purchase a new firearm. We are enthusiast after all.